Grass replaces plastic in take-away food packaging
Soon, packaging for take-away foods might be completely based on local, sustainable materials instead of fossil-based products. In a new research project, a packaging solution based on upcycled grass fibres is being developed.
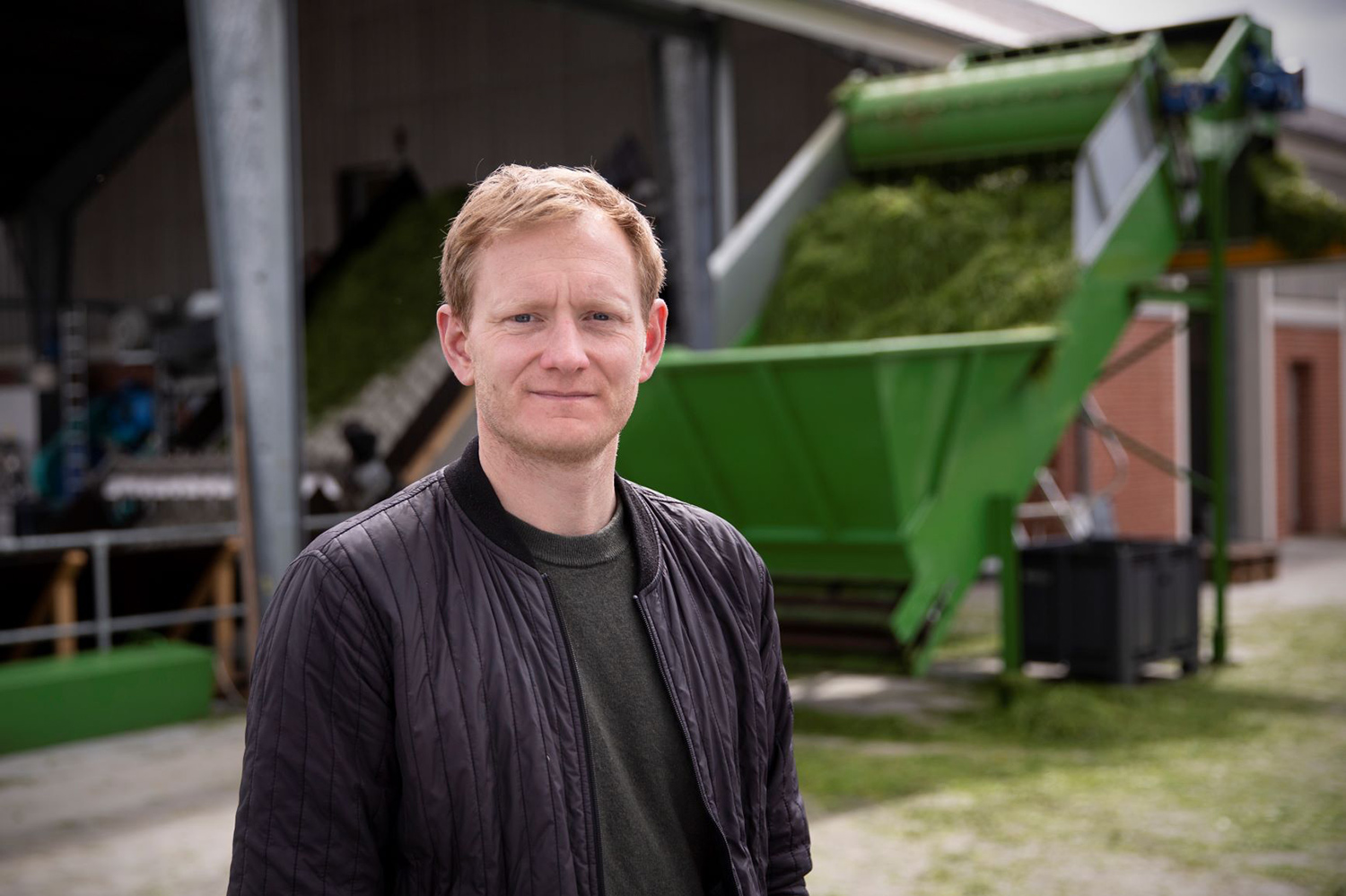
Grass fibres can replace plastic as a 100% biodegradable and disposable material for packaging for take-away food. This is the goal of the new innovative project SinProPack, which aims to develop a sustainable alternative to the disposable plastics currently used for packaging.
The project is bringing together industry, consumers and knowledge institutions to develop, demonstrate, test and evaluate fibre-based packaging for to-go food via proof-of-concept, pilot-scale trials and industrial upscaling.
"Disposable packaging made of grass brings a lot of environmental benefits. The packaging will be 100% biodegradable, so if someone accidentally drops their packaging in nature, it will decompose naturally," says Anne Christine Steenkjær Hastrup, centre director at Danish Technological Institute, who is coordinating the project.
Every year, Denmark consumes more than 10,000 tonnes of packaging for take-away food and drinks. Replacing 10,000 tonnes of disposable plastic with a corresponding quantity of bio-based and biodegradable packaging will reduce carbon emissions from packaging production by approx. 210,000 tonnes CO2 annually.
The project will form a basis for a paradigm shift in packaging solutions by introducing and demonstrating the possibilities of using green biomass for single-use packaging for food products, as well as a sustainable bioeconomy business model for the technology.
Green biomass is an easily accessible resource in Denmark, and green biorefining for protein production is already of considerable interest because of the proven high biomass yields, environmental effects and the potential to use untapped biomass from unproductive low-lying areas such as meadows.
"After we harvest the grass and extract the protein for animal feed, we can refine and pulp the grass fibres for cellulose, from which we can produce packaging. In this way, we can use and up-value a side stream from protein production. It’s a great way to create added value for biorefining, as not all grass fibre can necessarily be used as cattle feed," says Assistant Professor Morten Ambye-Jensen from the Department of Biological and Chemical Engineering at Aarhus University.
Fibres constitutes approx. 70 per cent of the grass fed into biorefining after protein has been extracted.
In the SinProPack project, the researchers will look at both grass and clover as fibre sources, as clover will be the primary biomass for future green biorefineries. However, the project will also take a closer look at the possibilities of using biomass harvested from peat soil, which is usually more fibrous and contains less protein.
The project entails testing and demonstrating the technology in the demo and pilot facilities at Aarhus University and Danish Technological Institute, and the company LEAF Packaging that already produce and manufacture 100% biodegradable fiber packaging for the food industry, will test and prove the grass fibre efficiency, stability and moldability on an industrial scale.
The project has received 3.3 MDKK (EUR 440K) in funding from the Green Development and Demonstration Programme, GUDP, under the Danish Agricultural Agency.
Additional information | |
We strive to ensure that all our articles live up to the Danish universities' principles for good research communication (scroll down to find the English version on the website). Because of this the article will be supplemented with the following information: | |
Funding | Funded by the Green Development and Demonstration Programme, GUDP, under the Danish Agricultural Agency with DKK 3.3 million (EUR 440K) |
Collaborators | Aarhus University, Danish Technological Institute (coordinator), LEAF Packaging ApS, COOP Danmark A/S |
Read more | Read more at the GUDP website |
Contact | Assistant Professor Morten Ambye-Jensen Department of Biological and Chemical Engineering, Aarhus University Tel.: +45 93508009 Mail: maj@bce.au.dk |