Wind turbine blades of the future will be recyclable
In the DreamWind project, researchers will develop a chemical substance that will make it possible to separate composite materials from each other. This means that the large and expensive fibreglass components from wind turbines will be recyclable in the future.
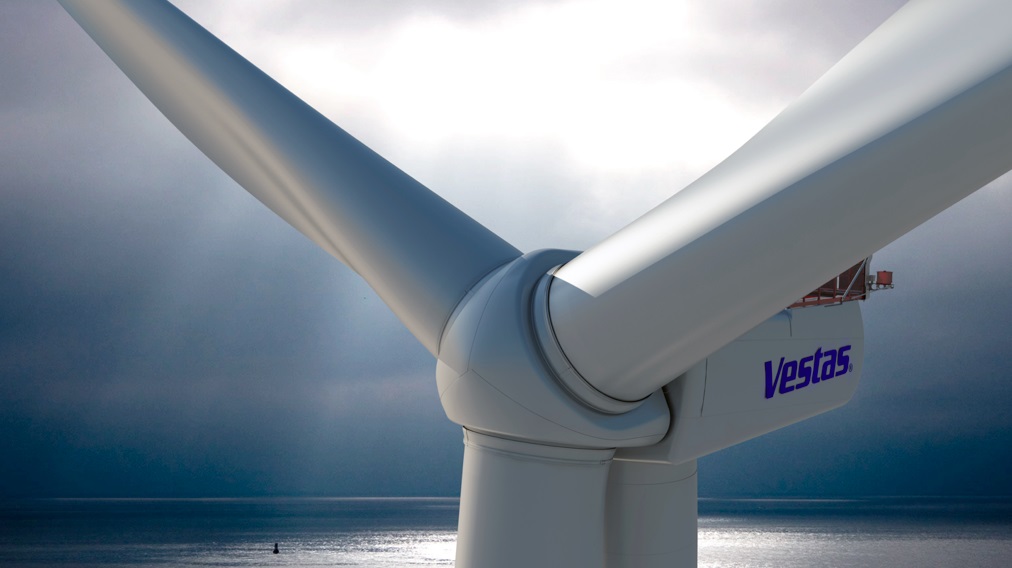
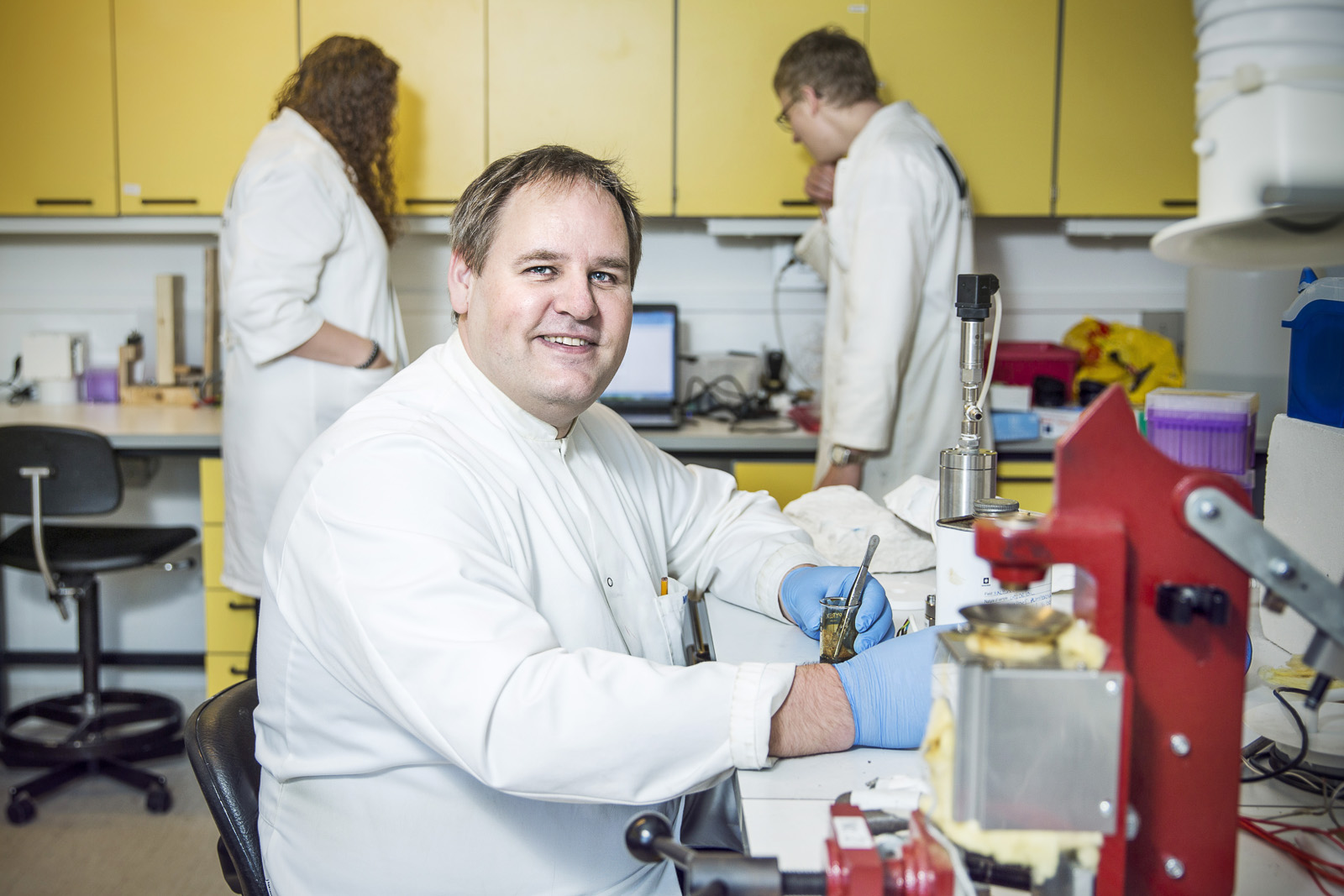
What do you do with a wind turbine that is no longer operational? This question is becoming more and more relevant as the expiration date is getting closer and closer for the wind turbines that were erected early on.
The first old wind turbines have already been scrapped, and this takes place at enormous ‘graveyards’. Here the components are crushed and buried in the ground because it is virtually impossible today to recycle the material, according to Associate Professor Mogens Hinge, Department of Engineering, Aarhus University.
“Components made of fibreglass have to go through a difficult procedure before they can be reused. This entails separating the glass from the plastic, and you can only do this if you heat the material for a long time at 600 degrees Celsius, which is far from profitable – from both an energy and an economic point of view,” he says.
Along with his research team and industrial experts, Associate Professor Hinge has specialised in developing nanobinders for a number of years.
The acute problem in the wind turbine industry inspired them to develop a solvent with the opposite properties, so that instead of binding materials to each other, it can separate them chemically with limited or no heating at all.
New binding agent for fibreglass
The researchers are initially focusing on designing an agent for fibreglass, and the first laboratory results are promising.
The idea is that the glass should be reused when it has been cleaned – for new fibreglass components for structures such as wind turbines, aircraft or cars.
“This way, we can retain the value of the material instead of just discarding it. The technology holds great potential for recycling,” says Associate Professor Hinge.
At the same time, the technology can save the wind turbine industry a considerable amount of money and reduce carbon dioxide emission.
“It’s expensive to manufacture fibreglass that can’t be recycled. It’s expensive to drive round with blades when they have to be scrapped. It’s expensive to smash them to pieces and bury them. Chemical research can provide the industry with an enormous boost of innovation,” he says.
Chemical research paves the way for more recycling
Innovation Fund Denmark has invested a total of DKK 17.6 million in the project, which in the long run can influence the recycling of composite materials outside the wind turbine industry.
“With the investment from Innovation Fund Denmark, we now have an opportunity to develop smart new materials that can change shape or separate as required when they’re no longer in use. This is an important project that could have a major impact on the way in which materials are recycled in the future,” says Professor Kim Daasbjerg, Department of Chemistry, Aarhus University.
In the DreamWind project, Aarhus University will collaborate with partners including Vestas Wind Systems A/S and the Danish Technological Institute to develop new composite materials for wind turbine blades.
The parties expect to be ready with a chemical compound for separating fibreglass within four years.
For more information, please contact