A longstanding mystery in manufacturing has been solved
A common aspect of most manufacturing processes is to shape components by removing chips from materials surface. Now, researchers from Aarhus University have experimented to find the perfect cutting process.
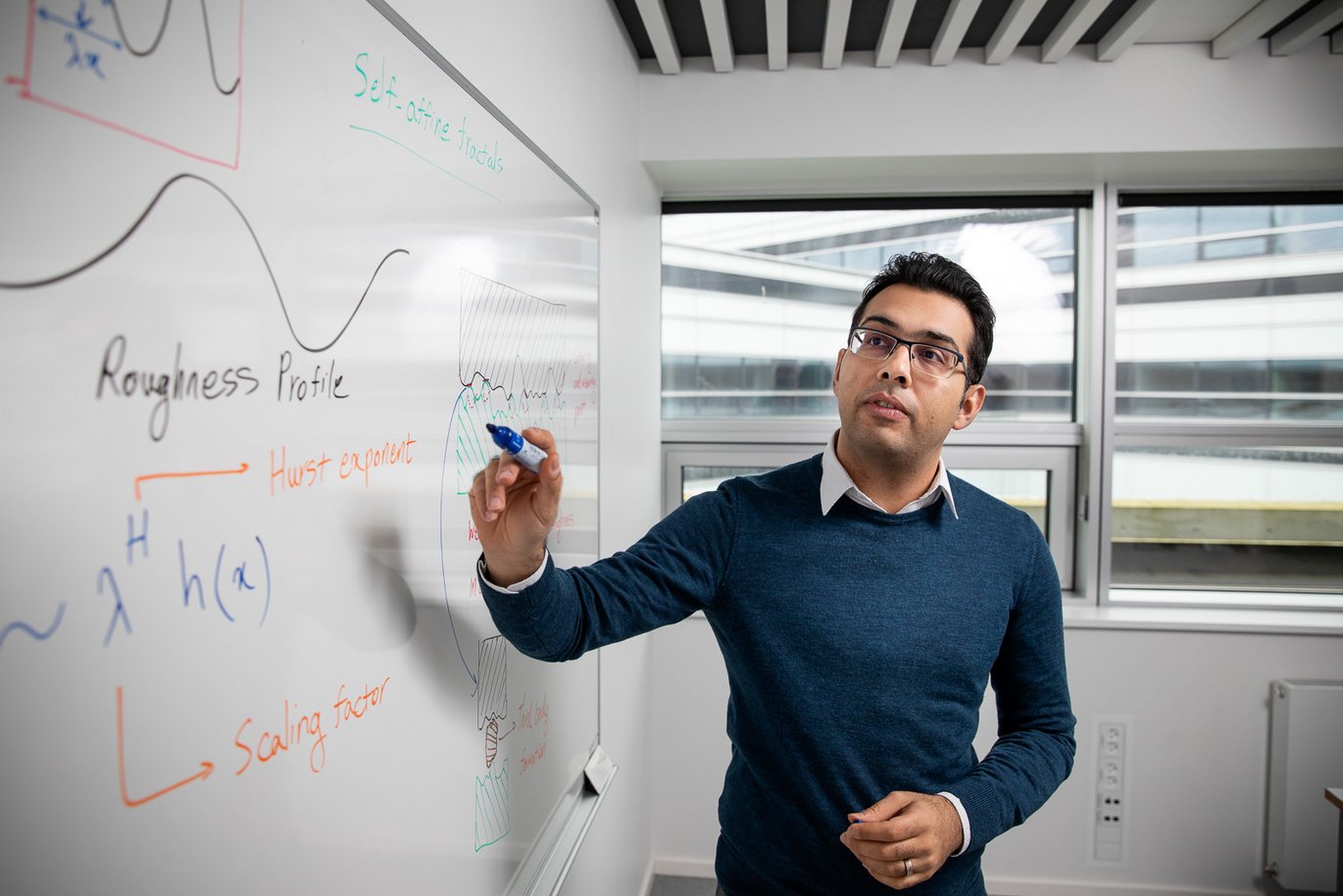
Worn-out industrial milling tools and damaged materials cost the manufacturing industry billions each year.
In manufacturing processes, components are shaped by removing chips from a bulk material, but a clear understanding of what factors control the size and shape of removed chips has remained elusive, limiting the manufacturing sector to incremental advancement based on trial-and-error approaches.
Making a perfect cut every time is desirable, and now researchers at Aarhus University have modelled and experimented their way to solve the long-standing challenge of finding a perfect cutting process that minimises tool wear and optimizes surface finish.
- ALSO READ: Breakthrough in groundwater measurements
"We have developed a simple analytical model that can predict the mechanism for chip formation and its transition for almost every material. The model reveals the existence of a critical cutting depth as a function of material properties, tool geometry and running conditions,” says Associate Professor Ramin Aghababaei who’s leading the research at Aarhus University.
The study has been published in the scientific journal Physical Review Letters and the research is part of the project Cutting-Edge.
Ramin Aghababaei continues:
“By testing on various plastic materials, we have found a critical cutting depth, below which we can remove long chips in a smooth and gradual way and above which short and irregularly-shaped chip formed in an abrupt manner.”
The associate professor points out that deviation from this critical cutting depth has a major impact on wear and tear of the tools used, on energy consumption, and on the final product finish.
"This breakthrough outcome is a result of having ambitious and professional partners in the project and this achievement cannot be obtained without their individual contribution. The team will continue to develop the model, but tool industry can start using it already to design optimal cutting tools,” he says.
The research forms part of the Grand Solutions project, Cutting-Edge, which aims to improve the performance of cutting tools for stainless steel processing. The project is being funded by the Innovation Fund Denmark with DKK 7 mio.
“The project is a collaboration between Aarhus University, Teknologisk Institut, Danish Advanced Manufacturing Research Center (DAMRC), V. Bech Tool Manufacturing A/S and three Danish manufacturers, TripleCut A/S, NSM A/S, and KAMF A/S.
Contact
Associate Professor Ramin Aghababaei
Aarhus University, Department of Mechanical and Production Engineering
Mail: ra@mpe.au.dk
Tel.: +4593508956