When less is more: Designer slits make glasslike materials much stronger
By making specially designed slits in Plexiglas, Danish researchers have made it stronger, lighter and more flexible. The new knowledge could be used to make microchips much more durable.
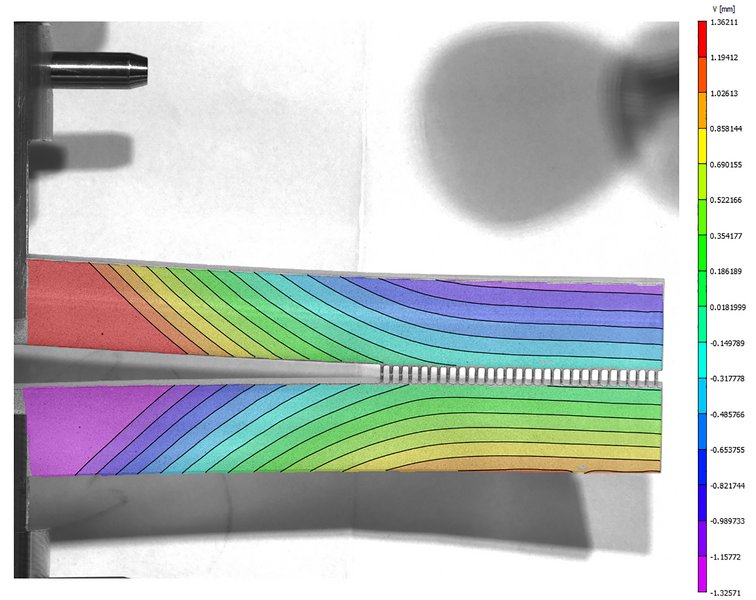
By cutting a geometric pattern in a material, researchers from Aarhus University and the Turner Research Group from the University of Pennsylvania in the US have changed the mechanical properties of the material and improved its tolerance against fracture.
In their experiment, the researchers used Plexiglas as a model material and added a number of specially designed cuts, in so doing removing some of the material. Plexiglas is usually brittle and glasslike, so it is vulnerable to fractures. With the new technique, the product becomes lighter than the original, stronger and more robust.
The technique produces what is called a mechanical metamaterial, meaning that the properties of the material are changed, solely by changing its geometric structure. Therefore, the material primarily derives its characteristics from the geometric structure rather than its chemical composition.
The discovery has been described in the renowned Journal of the Mechanics and Physics of Solids.
"In the project, we tested a geometric double cantilever beam shape, which can represent a wide range of products, including microchips. When manufacturing microchips, the component has a tendency to crack because it is made of a brittle material. By introducing these specially designed cuts, the component becomes more flexible and less fragile. The effect originates from the new geometry, which can spread stress loads over a larger area reducing the stress singularity responsible for formation and growth of cracks," says Simon Heide-Jørgensen, a postdoc and researcher on the project.
The research team made a number of laser cuts in the material, thereby changing its geometry near the expected stress singularities. This means that it is possible to make the material fracture by design (or on-demand), i.e. follow the cuts. This significantly increases the component's resistance to cracks and fracture.
"Instead of concentrating in a singularity, stresses now spread along the cuts we've made in the material. The material can withstand a greater load before breaking. When a fracture does arise, it will grow along the cuts, and this will slow it down and thereby inhibit further crack growth. The material obtains a greater tolerance to crack growth and it becomes much less fragile," says Simon Heide-Jørgensen.
In addition to making the material more resilient to cracks, the cuts make it more flexible and lighter, and, in principle, reduce material consumption.
Contact
Postdoc Simon Heide-Jørgensen
Department of Engineering, Aarhus University
shj@eng.au.dk
Tel.: +4560180352
Associate Professor Michal Budzik
Department of Engineering, Aarhus University
mibu@eng.au.dk
Tel.: +4541893217